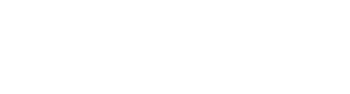

Material Cost

Written by True Tamplin, BSc, CEPF®
Reviewed by subject matter experts.
Updated on March 01, 2023
Get Any Financial Question Answered
Table of contents, material cost: definition.
Material is the most important element of cost . In most manufacturing organizations, 50% to 70% of the total cost of a product is represented by the cost of the material.
Material cost was defined by the Institute of Cost and Management Accountants as follows: “the cost of commodities supplied to an undertaking.”
Examples of material cost include:
- Cost of cotton or cotton yarn for a textile mill
- Cost of cotton cloth for a hosiery factory
- Cost of wood, other raw materials, and factory supplies for a furniture manufacturer
Types of Materials
Materials are either direct materials or indirect materials.
Direct Materials
The characteristics of direct materials are the following:
- Directly related to and identified with cost centers or cost units . In other words, these are the items that form part of the product itself (e.g., cotton used for spinning cotton yarn, wood used in making furniture, or leather used in shoe-making).
- Purchased for a particular job, work order, or contract.
- Finished product of a particular process that forms the raw material of the succeeding process (e.g., cost of yarn transferred from the spinning process to weaving process).
Indirect Materials
The characteristics of indirect materials are the following:
- Cannot be allocated but can be apportioned to (or absorbed by) cost centers or cost units. Examples include cotton waste to clean machinery, lubricants for oiling machinery, and diesel oil to generate power.
- Used in such small quantities that it is not possible to ascertain their per-unit cost exactly (e.g., the cost of thread and nails used in shoe-making).
Material Cost FAQs
What are the different types of material costs.
The different types of material costs include raw materials, components and sub-assemblies, hardware, inventory parts and supplies, packaging and labeling materials, shipping costs, and taxes related to these items.
How is material cost calculated?
Material cost is typically calculated by multiplying the unit price for each type of material used in a product or project by the quantity required for its completion.
What is included in a material cost estimate?
A material cost estimate should include all necessary components required to complete the job such as raw materials, components and sub-assemblies, hardware, inventory parts and supplies, packaging and labeling materials, shipping costs, taxes, and any additional fees associated with the project.
How does material cost affect profit margin?
Material cost is an important factor in determining a company’s profit margin as it directly affects the total cost of production. Therefore, reducing material costs can often result in increased profits for the business.
What strategies can be used to control material costs?
Strategies used to control material costs include negotiating better prices with suppliers, using lean manufacturing principles to reduce waste and optimize processes, and implementing Just-In-Time inventory systems to reduce excess inventory carrying costs. Additionally, companies should also look into recycling or reusing materials whenever possible.

About the Author
True Tamplin, BSc, CEPF®
True Tamplin is a published author, public speaker, CEO of UpDigital, and founder of Finance Strategists.
True is a Certified Educator in Personal Finance (CEPF®), author of The Handy Financial Ratios Guide , a member of the Society for Advancing Business Editing and Writing, contributes to his financial education site, Finance Strategists, and has spoken to various financial communities such as the CFA Institute, as well as university students like his Alma mater, Biola University , where he received a bachelor of science in business and data analytics.
To learn more about True, visit his personal website or view his author profiles on Amazon , Nasdaq and Forbes .
Related Topics
- ABC Analysis
- Apportionment of Joint Cost of Materials
- Classification and Codification of Materials
- Contract Account
- Contract Costing
- Cost Plus Contract
- Cost Price Method
- Cumulative Average-Time Learning Model
- Direct Materials Cost
- Direct Materials Inventory
- Economic Order Quantity (EOQ)
- Economic Order Quantity (EOQ): Practical Problems and Solutions
- First In, First Out (FIFO) Method Problem and Solution
- Goods in Transit
- How to Calculate Profit and Loss on Contracts
- Incremental Unit-Time Learning Model
- Inspection and Storage of Materials
- Inventory Turnover Ratio
- Last In, First Out (LIFO) Method Problem and Solution
- Material Abstract
- Material Control
- Material Costing: Practical Problems and Solutions
- Material Ledger Card
- Material Requisition
- Material Return Note
- Maximum Stock Level
- Methods and Principles of Codification of Materials
- Minimum Stock Level or Minimum Stock Limit
- Periodic Inventory System
- Pricing Methods of Material Issued
Ask a Financial Professional Any Question
We use cookies to ensure that we give you the best experience on our website. If you continue to use this site we will assume that you are happy with it.
Fact Checked
At Finance Strategists, we partner with financial experts to ensure the accuracy of our financial content.
Our team of reviewers are established professionals with decades of experience in areas of personal finance and hold many advanced degrees and certifications.
They regularly contribute to top tier financial publications, such as The Wall Street Journal, U.S. News & World Report, Reuters, Morning Star, Yahoo Finance, Bloomberg, Marketwatch, Investopedia, TheStreet.com, Motley Fool, CNBC, and many others.
This team of experts helps Finance Strategists maintain the highest level of accuracy and professionalism possible.
Why You Can Trust Finance Strategists
Finance Strategists is a leading financial education organization that connects people with financial professionals, priding itself on providing accurate and reliable financial information to millions of readers each year.
We follow strict ethical journalism practices, which includes presenting unbiased information and citing reliable, attributed resources.
Our goal is to deliver the most understandable and comprehensive explanations of financial topics using simple writing complemented by helpful graphics and animation videos.
Our writing and editorial staff are a team of experts holding advanced financial designations and have written for most major financial media publications. Our work has been directly cited by organizations including Entrepreneur, Business Insider, Investopedia, Forbes, CNBC, and many others.
Our mission is to empower readers with the most factual and reliable financial information possible to help them make informed decisions for their individual needs.
How It Works
Step 1 of 3, ask any financial question.
Ask a question about your financial situation providing as much detail as possible. Your information is kept secure and not shared unless you specify.

Step 2 of 3
Our team will connect you with a vetted, trusted professional.
Someone on our team will connect you with a financial professional in our network holding the correct designation and expertise.

Step 3 of 3
Get your questions answered and book a free call if necessary.
A financial professional will offer guidance based on the information provided and offer a no-obligation call to better understand your situation.

Where Should We Send Your Answer?
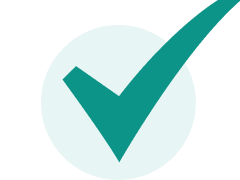
Just a Few More Details
We need just a bit more info from you to direct your question to the right person.
Tell Us More About Yourself
Is there any other context you can provide.
Pro tip: Professionals are more likely to answer questions when background and context is given. The more details you provide, the faster and more thorough reply you'll receive.
What is your age?
Are you married, do you own your home.
- Owned outright
- Owned with a mortgage
Do you have any children under 18?
- Yes, 3 or more
What is the approximate value of your cash savings and other investments?
- $50k - $250k
- $250k - $1m
Pro tip: A portfolio often becomes more complicated when it has more investable assets. Please answer this question to help us connect you with the right professional.
Would you prefer to work with a financial professional remotely or in-person?
- I would prefer remote (video call, etc.)
- I would prefer in-person
- I don't mind, either are fine
What's your zip code?
- I'm not in the U.S.
Submit to get your question answered.
A financial professional will be in touch to help you shortly.
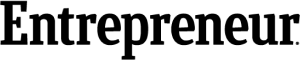
Part 1: Tell Us More About Yourself
Do you own a business, which activity is most important to you during retirement.
- Giving back / charity
- Spending time with family and friends
- Pursuing hobbies
Part 2: Your Current Nest Egg
Part 3: confidence going into retirement, how comfortable are you with investing.
- Very comfortable
- Somewhat comfortable
- Not comfortable at all
How confident are you in your long term financial plan?
- Very confident
- Somewhat confident
- Not confident / I don't have a plan
What is your risk tolerance?
How much are you saving for retirement each month.
- None currently
- Minimal: $50 - $200
- Steady Saver: $200 - $500
- Serious Planner: $500 - $1,000
- Aggressive Saver: $1,000+
How much will you need each month during retirement?
- Bare Necessities: $1,500 - $2,500
- Moderate Comfort: $2,500 - $3,500
- Comfortable Lifestyle: $3,500 - $5,500
- Affluent Living: $5,500 - $8,000
- Luxury Lifestyle: $8,000+
Part 4: Getting Your Retirement Ready
What is your current financial priority.
- Getting out of debt
- Growing my wealth
- Protecting my wealth
Do you already work with a financial advisor?
Which of these is most important for your financial advisor to have.
- Tax planning expertise
- Investment management expertise
- Estate planning expertise
- None of the above
Where should we send your answer?
Submit to get your retirement-readiness report., get in touch with, great the financial professional will get back to you soon., where should we send the downloadable file, great hit “submit” and an advisor will send you the guide shortly., create a free account and ask any financial question, learn at your own pace with our free courses.
Take self-paced courses to master the fundamentals of finance and connect with like-minded individuals.
Get Started
To ensure one vote per person, please include the following info, great thank you for voting., get in touch with a financial advisor, submit your info below and someone will get back to you shortly..
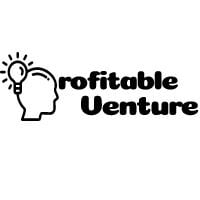
What is the Cost Structure in a Business Plan?
By: Author Tony Martins Ajaero
Home » Business Plans
Cost structure in a business plan refers to a section in the business plan where all the necessary costs or expenses expected to be incurred to attain the desired objective noted in the business plan are explicitly outlined.
Depending on the objective of the business plan, these costs may include the cost of purchasing the raw material, the cost of marketing, or even the cost of packaging the finished products. Note that starting or running a business will involve some kind of cost, and this is what is noted in the cost structure of the business plan.
It is imperative to note that cost structures differ between retailers and service providers, therefore the expense accounts noted in a business plan will depend on the cost objects, such as a product, service, project, customer, or business activity.
Suggested for You
- 13 Best Companies That Offer Business Plan Writing Services
- 27 Best Business Plan Writing Software Online (FREE & Paid)
- 13 Best Business Plan Writing App for Android and iPad
- 26 Best LivePlan Alternatives (FREE & Paid)
- Which Two Documents Summarizes the Business Plan of a Company?
Even within a company, note that cost structure may vary between product lines, divisions, or business units, owing to the varying types of activities they perform. Howbeit, the primary components of any cost structure are variable and fixed costs.
Variable costs refer to costs that alter in direct proportion to production/selling activities. These costs may include sales commissions, product costs, cost of labor and raw materials used in manufacturing, etc. Fixed costs refer to those that stay the same regardless of the volume of sales or business activity.
They are costs that accumulate owing to the passage of time such as insurance, salaries, and rent. A good number of individuals believe that as long as a business makes the same amount of profit as another business with similar operations, the cost structure they leverage makes no difference.
However, an analysis of what occurs to a business’ break-even point when there are alterations to its cost structure reveals the difference. Therefore, when making financial projections for a new business, it is advisable you keep the fixed costs at the barest minimum so that the break-even point can be reached much sooner.
How to Write the Cost Structure in a Business Plan
To ensure you can maximize the profits of your business, it is imperative you understand all the costs associated with starting and running your business, and also seek ways to reduce them to the minimum. Below is a detailed guideline on how to write the cost structure section of your business plan.
Make a Summary of Your Costs and Expenditure
While you will most often note your costs in your financial tables, it is recommended you give a summary of your main costs and timescales for expenditure. This will help buttress how your business will function within the next few years. To do this, take your time to analyze all attributed ‘fixed’ costs and ‘variable’ costs as they can help plan your cash flow.
- Fixed costs : These are the regular or one-off payments that have been concluded in advance, for example, rent, insurance, and subscriptions. You can review these annually to validate that you’re getting a good deal.
- Variable costs : Note that these are predictable costs that can change owing to your business activity and volume of sales. For businesses selling products, variable costs might include direct materials, commissions, and piece-rate wages. For service providers, variable expenses are composed of wages, bonuses, and travel costs.
While making a summary of your cost and expenses, it is recommended you show that your costs align with your activity – costs will most likely increase as your activity increases or as your sales volume goes up. Also note that you may have to employ more staff, move to a larger business facility or obtain more supplies.
Also note that things like insurance will be more costly as you employ more staff and more customers, therefore take heed that it is reflected in your cost summary and your cash flow.
Make a Concise Description of Your Main Sources of Income
The next step will be to declare whether you have secured the income (for instance, a grant or contract that has already been concluded) or if it is an income forecast (for instance, sales of your new product or service).
If you intend to depend on one source, then you must note any plans you have to diversify your income or what you intend to do if you lose that income source. If you have or are applying for loans or social investment, make sure you describe in clear detail your plans for repayment.
Describe Your Pricing Strategy
Depending on the type of business or your objective for putting together the business plan, consider using this section to note your pricing strategy. Have in mind there are numerous ways to set a price for your product or service.
- Mark up : Understand the price the product or service costs you, then add a percentage to get the final price (e.g. cost + 10%).
- Going rate : Take your time to research the competition to understand what a typical price is and try to match it.
- Market-oriented : Set the price based on research with your target market and what is obtainable in your market.
- Perceived value : Consider the value the consumer places on a product. Note that this may be more than the product is actually worth. For instance, people are known to pay more for branded goods even though the product is more or less the same as a non-branded item because they perceive it to be better or higher quality.
- Pricing schemes : You may also choose to make available discounts for certain groups, or for early-bird payment, bulk purchases, or off-peak use.
It is important to note that expensive items are seen to be more valuable, and a good number of voluntary organizations underestimate the value of their work. Any successful business activity will have to give a surplus between the price and the cost, and your costs may be higher than what is common in the market. Also, take your time to work out how much it costs to deliver your product or service before you set your price.
The cost structure is mostly attributed to all the costs that can be incurred while working on the goal of the business plan. Always remember that the aim of a cost structure in your business plan is to note the funds you need during the business process or for the business as a whole. It is primarily to allocate the costs in such a way that the costs would be minimized and the profits earned effectively maximized.
- High School
- You don't have any recent items yet.
- You don't have any courses yet.
- You don't have any books yet.
- You don't have any Studylists yet.
- Information
Business Plan Chapter 5
Bachelor of science in accoutancy (bsa), san pedro college of business administration.
Recommended for you
Students also viewed.
- BIR FORM 0605 - example only
- Sample Tagalog Demand Letter
- ACFr Og CUr Ok 4ju RBl U-4Yz FHo RUl 9S6u5z-39znj PBw Yq QJf E 4mo Pfq Gfu Hl 5p UNz3Rw B-rbo Oq 0Ks2M3hy9 Icuftbcnp EBIR 78 8Gyk QQs LOmky 9ng KNf D-o4Co8OJRVw 9f4er7OEu V5m Krtir
- Essential of accounting 2 activities
- Maya Credit So A 87cd078e2eb7463685 fc9432897 e624f 2023AUG 2
- 2551Q - Tax Form
Related documents
- Wayang Shadow Puppet Resouce
- Midterm SM - notes
- Individual AND DUAL Sports Prelim
- Finals PP - notes
- The Need for Management Information Systems on Strategic Planning Process in Libyan Health Service Organizations-C016811326
- R2S 107 Perceived effects of work from office and telecommuting on the work performance of accountants
Preview text
Raw Materials
Raw materials are materials or substances used in the primary production or manufacturing of goods. Raw materials are often referred to as commodities, which are bought and sold on commodities exchanges worldwide. Raw materials are bought and sold in what is called the factor market because raw materials are factors of production along with labor and capital.
Table 6 Raw Materials
Particulars Qty.
Measurement
Unit Cost Total Cost
All purpose flour 8 Kilograms ₱ 11 per ¼ kilograms
Margarine 8 Kilograms ₱15 per ¼ kilograms
Sugar 8 Kilograms ₱ 12 per ¼ kilograms
Skim Milk 8 Kilograms ₱15 per ¼ kilograms
Matcha Powder 1 Kilograms ₱ 300 per 1 kilograms
Total Direct Materials ₱652.
Table 6 shows the direct materials that will be used in the operation of the service and the service proper together with its unit and total cost.
- Multiple Choice
Course : Bachelor of Science in Accoutancy (BSA)
University : san pedro college of business administration.

- More from: Bachelor of Science in Accoutancy BSA San Pedro College of Business Administration 359 Documents Go to course
- Starting a Business
- Growing a Business
- Business News
- Science & Technology
- Money & Finance
- For Subscribers
- Write for Entrepreneur
- Tips White Papers
- Entrepreneur Store
- United States
- Asia Pacific
- Middle East
- United Kingdom
- South Africa
Copyright © 2024 Entrepreneur Media, LLC All rights reserved. Entrepreneur® and its related marks are registered trademarks of Entrepreneur Media LLC
How to List Personnel and Materials in Your Business Plan Manufacturers must show the labor and resources needed to run their business. Here's what you need to know.
By Eric Butow
Opinions expressed by Entrepreneur contributors are their own.
This is part 11 / 12 of Write Your Business Plan: Section 5: Organizing Operations and Finances series.
Manufacturers combine labor and materials to produce products. Any problems with these critical inputs spell trouble for your business and its backers. Business plan readers look for solid systems to ensure that personnel and materials are appropriately abundant.
For this reason, your plan should show that you have adequate, reliable sources of supply for the materials you need to build your products. If you are working with suppliers in other parts of the world, show that they are reliable and that you have established a system to make such international production run smoothly. A global marketplace means more opportunities to find the materials or products you need and new markets for sales. This can be impressive to your readers.
Related: The Main Objectives of a Business Plan
However, you need to define and provide the details of how your business will benefit from being a part of the global marketplace. Even if you are not planning to actively pursue global partnerships, buy from vendors around the globe, or market to customers in other countries, you must address the possibility of international sales if you are selling via your website.
Estimate your needs for materials and describe the agreements with suppliers, including the length and terms you have arranged to fulfill those needs. You may also give the backgrounds of your major suppliers and show that you have backup sources available should problems develop.
Related: What Equipment and Facilities to Include in Your Business Plan
You'll first need to estimate the number and type of people you will require to run your plan. Startups can do this by looking at competitors' plants or by relying on the founders' prior experience at other companies. Existing firms can extrapolate what they'll need to expand from current operations.
Next, show that you can reasonably expect to be able to hire what you need. Look at local labor pools, unemployment rates, and wage levels using information from chambers of commerce or similar entities. If you plan to import sizable numbers of workers, check out housing availability and build an expense for moving costs into your budget.
Related: How to Craft a Business Plan That Will Turn Investors' Heads
Entrepreneur Leadership Network® VIP
Owner of Butow Communications Group
Editor's Pick Red Arrow
- Lock I Started a Business to Streamline the $90 Trillion Wealth Transfer From Boomers to Younger Generations — Here's How It Helps People Receive Inheritances Faster
- Is ChatGPT Search Better Than Google? I Tried the New Search Engine to Find Out.
- This Couple Wanted to Make an Everyday Household Product 'Unquestionably Better.' Now Their Business Sees Over $200 Million Annual Revenue : 'Obliterated Our Goals.'
- Lock AI Could Ruin Your Life or Business — Unless You Take These Critical Steps
- Taco Bell Is Launching Chicken Nuggets — Here's When and Where to Get Yours
- Lock After This 26-Year-Old Got Hooked on ChatGPT, He Built a 'Simple' Side Hustle Around the Bot That Brings In $4,000 a Month
Most Popular Red Arrow
Oscar mayer is hiring drivers for its famous wienermobile. here's how to apply and how much you'll get paid..
The one-year gig is a coveted role—only 1% of applicants become "hotdoggers."
The Fed Just Cut Rates for the Third Time This Year. Here's How It Will Affect Mortgage Rates, According to a 40-Year Veteran of the Real Estate Industry
The target range for the federal funds rate is now 4.25% to 4.5%.
OpenAI Employees Could Become Multimillionaires Next Week Thanks to a New Stock Sale
OpenAI employees can cash out on millions of dollars worth of stock.
'Wanted to Cry for Joy': MacKenzie Scott Donates $65M Gift to Housing Nonprofit
It was Scott's second donation to the nonprofit and a complete surprise.
63 Small Business Ideas to Start in 2024
We put together a list of the best, most profitable small business ideas for entrepreneurs to pursue in 2024.
'Now Accepting Applications': Elon Musk Is Opening a New Preschool in Texas Called Ad Astra. Here's How to Apply.
The school got an official permit last month to operate with as many as 21 students.
Successfully copied link


Essential Operating Expenses for Building Material Businesses

- 5-Year Excel
- MAC & PC Compatible
- Immediate Download
Related Blogs
- How to Increase Profits in Your Building Material Business
- Top Startup Costs for a Building Material Production Company
- Essential KPIs for Building Material Production
- Start a Building Material Production Business: A Step-by-Step Guide
- How to Prepare for Business Plan Success in Building Material Production
Are you aware of the top nine operating costs that can make or break a building material production business? From raw materials to labor , understanding these expenses is crucial for maintaining profitability. Curious about how to streamline your budget? Discover effective strategies to minimize costs and boost efficiency in your operations by exploring our comprehensive business plan .
How Much Does It Cost To Operate A Building Material Production Company?
Operating a building material production company, such as EcoBuild Innovations , involves a complex cost structure that can significantly impact overall profitability. On average, the total operating costs for a building materials business can range from $500,000 to over $5 million annually , depending on the scale and type of materials produced.
The cost analysis of building material production typically includes fixed and variable expenses that must be carefully managed to ensure sustainability and profitability. Key components of these costs include:
- Raw Material Costs: These can account for 40-60% of total production expenses, depending on the materials used.
- Labor Costs: On average, labor expenses in manufacturing can represent 20-30% of operational costs.
- Utilities and Energy Costs: Energy consumption costs in production can vary greatly, often reaching 10-20% of overall costs.
- Maintenance and Equipment Costs: Regular maintenance is essential, and these costs can be 5-10% of operational budgets.
- Transportation and Logistics Costs: These costs are critical for supply chain management and can take up 5-15% of total expenses.
- Insurance Costs: Protecting the business can cost 1-3% of total revenue.
- Waste Management Costs: Proper waste disposal and recycling can add up to 2-5% of operational costs.
- Regulatory Compliance Costs: Adhering to regulations often incurs additional expenses, approximately 2-4% of operational budgets.
- Research and Development Costs: Investing in innovative, eco-friendly materials can consume 3-7% of operational expenses.
Understanding these top operating expenses for building materials is crucial for effective cost management. For instance, the breakdown of manufacturing overhead costs can provide insights into areas where efficiency can be improved.
Tips for Managing Operational Costs
- Conduct regular reviews of raw material cost estimation to identify potential savings.
- Invest in energy-efficient machinery to lower energy consumption costs in production .
- Optimize logistics routes to reduce logistics costs in construction materials .
By focusing on these aspects, building material production companies can better navigate the financial landscape and enhance their operational efficiency, ensuring a sustainable and profitable future in the industry. For more detailed insights on calculating these costs, you can refer to resources such as this guide .
What Are The Largest Operating Costs Of A Building Material Production Company?
In the building material production industry, understanding the largest operating costs is essential for financial stability and long-term success. The following key expenses dominate the budget of companies like EcoBuild Innovations, especially as it strives to provide sustainable alternatives in the construction sector:
- Raw Material Costs: These typically represent the most significant share of production expenses, accounting for approximately 40-60% of total operating costs. This includes costs for sourcing sustainable materials that align with EcoBuild's eco-friendly focus.
- Labor Costs: Labor expenses often range from 20-30% of total operating costs. This encompasses wages, benefits, and training costs for skilled workers necessary for operating machinery and ensuring quality control.
- Utilities and Energy Costs: With energy consumption closely tied to manufacturing processes, utilities can account for about 5-10% of costs. Implementing energy-efficient technologies may help mitigate these expenses.
- Maintenance and Equipment Costs: Regular maintenance is crucial for operational efficiency and can represent around 5-10% of operating costs. Investing in durable equipment can reduce long-term maintenance needs.
- Transportation and Logistics Costs: The logistics of delivering materials to clients and transporting raw materials contributes to 5-10% of expenses. Strategic partnerships with local suppliers can help reduce these costs.
- Insurance Costs: Depending on the scale of production, insurance may account for around 2-5% of overall costs. This is vital in mitigating risks associated with production and delivery.
- Waste Management Costs: This can represent 3-5% of operating expenses. Implementing sustainable waste management practices is not only cost-effective but also aligns with EcoBuild's mission.
- Regulatory Compliance Costs: Compliance with industry regulations and environmental standards can add 2-4% to operational costs. It's important for EcoBuild to stay up to date with regulations to avoid penalties.
- Research and Development Costs: Investing in R&D to develop innovative, sustainable materials can be costly, typically consuming around 3-6% of operating costs. However, this investment is crucial for staying competitive in the evolving market.
Tips for Managing Operating Costs
- Consider bulk purchasing raw materials to leverage economies of scale and reduce costs.
- Invest in employee training to enhance productivity and reduce labor expenses.
- Implement energy-efficient systems to cut down on utility costs.
By closely monitoring these operating expenses, EcoBuild Innovations can strategically manage its financial resources, ensuring a sustainable and profitable business model in the green construction material landscape.
How To Reduce Operational Costs For A Building Material Production Company?
Reducing operational costs in a building material production company, such as EcoBuild Innovations , is crucial to maintaining profitability and fostering sustainable growth. By focusing on key areas of production and supply chain management, businesses can significantly enhance their cost efficiency. Below are some effective strategies to consider:
Invest in Technology
- Implement automated systems to streamline manufacturing processes, which can reduce labor expenses by up to 30% .
- Utilize data analytics for precise cost management, helping to identify inefficiencies and improve decision-making.
Optimize Raw Material Sourcing
- Establish relationships with multiple suppliers to ensure competitive pricing and reduce raw material cost estimation by 10-15% .
- Consider alternative, sustainable materials that may have lower costs and positive environmental impacts.
Enhance Energy Efficiency
- Adopt energy-efficient machinery to decrease energy consumption costs in production by as much as 20% .
- Invest in renewable energy sources, such as solar panels, to stabilize long-term utility expenses.
Streamline Logistics and Transportation
- Optimize routing and load planning to lower logistics costs in construction materials, potentially saving 15% on transportation expenses.
- Use local suppliers when possible to minimize shipping costs and enhance supply chain sustainability.
By applying these strategies, building material production companies can effectively manage operational costs, ensuring a leaner production model while aligning with environmental sustainability goals. For further insights and metrics on the operational costs in building material production, consider exploring detailed cost analyses and benchmarks in the industry.
Operating Costs Examples For A Building Material Production Company
When launching a business in building material production , understanding the operating costs is crucial for profitability and sustainability. The costs associated with running a business like EcoBuild Innovations include a variety of fixed and variable expenses that can greatly influence the cost analysis of building material production .
Examples of Major Operating Costs
Here are some primary examples of operating costs that can affect a building material production company:
- Raw Material Costs: The procurement of raw materials, such as eco-friendly aggregates and sustainable polymers, can account for up to 60% of total production costs .
- Labor Costs: Labor expenses, including wages, benefits, and training, typically represent around 20-30% of operating costs . Skilled labor is essential for maintaining quality standards.
- Utilities and Energy Costs: Manufacturing processes are often energy-intensive. Energy consumption costs may reach 15% or more, depending on the technology employed.
- Maintenance and Equipment Costs: Regular maintenance and repair of machinery can incur costs of about 10% of total operating expenditures , critical for sustaining operational efficiency.
- Transportation and Logistics Costs: Distributing products to clients can push logistics costs up to 10-15% , particularly if raw materials are sourced from distant locations.
- Insurance Costs: Coverage for facilities and equipment typically falls within the 2-5% range of overall expenses, protecting against unforeseen incidents.
- Waste Management Costs: As a sustainable provider, EcoBuild Innovations must invest in waste management strategies, which could range from 3-7% of operational costs.
- Regulatory Compliance Costs: Ensuring compliance with environmental regulations can escalate costs to an extent of 2-4% but is essential for avoiding penalties.
- Research and Development Costs: Innovating new sustainable materials may require an investment of about 5-10% of revenues, essential for competitive advantage.
- Conduct regular cost audits to identify areas for potential savings.
- Invest in energy-efficient machinery to reduce utility expenses over time.
- Negotiate bulk purchase agreements for raw materials to lower costs.
- Implement lean manufacturing techniques to optimize labor and materials.
- Utilize technology for logistics to streamline transportation costs.
In the evolving landscape of building material production , it’s vital for companies like EcoBuild Innovations to stay ahead of these operational costs through effective management strategies. By understanding the production cost structure and carefully tracking business costs for building material companies , organizations can enhance their financial stability and sustainability efforts.
Which Running Costs Of A Building Material Production Company Are Fixed Expenses, And Why?
In the context of building material production operating costs , understanding the distinction between fixed and variable expenses is crucial for effective financial management. Fixed expenses are those costs that remain relatively stable regardless of the production volume, making them essential for budgeting and cost control.
The primary fixed expenses in a building material production company, such as EcoBuild Innovations, include:
- Rent or Mortgage Payments: The cost of leasing or owning a production facility constitutes a significant fixed expense. This can range from $5,000 to $50,000 per month depending on the location and facility size.
- Salaries for Permanent Staff: While labor costs can fluctuate, salaries for management and key personnel are fixed. Typically, these salaries constitute about 20% to 30% of total operating costs.
- Insurance Premiums: Business insurance, including liability and property coverage, is a necessary fixed cost that could range from $1,200 to $5,000 annually .
- Depreciation of Equipment: Machinery used in the production process incurs depreciation costs, which are fixed expenses calculated based on the machinery's useful life.
- Lease Payments for Equipment: If equipment is leased rather than purchased, the lease payments represent a significant fixed cost, often $1,000 to $10,000 per month .
- Utilities Base Costs: While utility costs can vary, there is typically a base charge that constitutes a fixed expense, making up approximately 5% to 10% of total operational expenses.
These fixed expenses play a vital role in the overall cost analysis of building material production. They contribute to the cost management in construction by providing a consistent financial baseline. Understanding these costs allows businesses like EcoBuild Innovations to focus on strategies for reducing variable costs, ensuring profitability even in fluctuating market conditions.
Tips for Managing Fixed Expenses
- Regularly review lease agreements to ensure competitive rates, especially as market conditions change.
- Implement energy-efficient practices to reduce utility base costs.
- Consider investing in equipment that offers long-term savings despite higher upfront costs.
By controlling these fixed expenses, companies within the building material production sector can enhance their financial sustainability and adapt more effectively to market dynamics, ultimately positioning themselves as leaders in sustainable construction solutions.
Which Operating Costs Of A Building Material Production Company Are Variable Costs, And Why?
In the realm of building material production , understanding which costs are variable is crucial for effective cost management . Variable costs fluctuate based on the level of production—more output leads to higher expenses, while reduced output brings those costs down. Here are the primary variable costs associated with a building material production company:
- Raw Material Costs: These are often the largest variable expenses. For instance, if EcoBuild Innovations produces eco-friendly concrete, the prices for aggregates and recycled materials can vary significantly, resulting in a cost range from $30 to $100 per ton , depending on the material source and market demand.
- Labor Costs: Labor expenses can also be variable, particularly for hourly workers involved in production. During peak seasons, companies might increase their workforce, leading to an uptick in labor costs. On average, manufacturing labor can account for approximately 20-30% of total production costs.
- Utilities and Energy Costs: As production volume increases, so do energy needs. For instance, energy costs may escalate from $2,000 to $10,000 per month based on operational scales, making them variable expenses.
- Transportation and Logistics Costs: These costs vary with the amount of product being shipped. For example, shipment of materials can cost between $0.50 to $2.00 per mile , depending on logistics providers and distance.
- Maintenance and Equipment Costs: While some maintenance costs can be fixed, those related to repairs often vary with usage. An increase in production may lead to more frequent repairs and downtime, raising costs temporarily.
Variable costs are pivotal to understanding the financial analysis of a building material production business. Effectively monitoring these costs can help in reducing operational expenses and maximizing profitability.
Tips for Managing Variable Costs
- Implement inventory management systems to optimize raw material usage .
- Invest in energy-efficient machinery to help reduce variable utility costs.
- Utilize software to track and manage labor hours effectively.
A comprehensive cost analysis of building material production will illustrate how these variable costs impact the overall operational expenses. To gain further insights on cost structures, consider visiting articles focused on building material production metrics .
What Are The Operating Expenses Of A Building Material Production Company?
In the competitive landscape of building material production, understanding the operating expenses is crucial for effective cost management. For companies like EcoBuild Innovations, which focus on sustainable alternatives, a thorough analysis of these costs can reveal opportunities for improvement and savings. Let's delve into the primary operating expenses faced by a building material production company.
- Raw Material Costs: Representing a significant portion of production expenses, raw materials account for approximately 50-70% of total costs. Sourcing quality, sustainable materials can impact both expenses and product offerings.
- Labor Costs: With the average labor expenses in manufacturing typically ranging from 20-30% of operational costs, investing in skilled labor is essential for quality production.
- Utilities and Energy Costs: Energy consumption can be a major expense, often comprising around 5-15% of total costs, especially in energy-intensive processes like mixing and curing materials.
- Maintenance and Equipment Costs: Regular maintenance and replacement of equipment can incur 5-10% of total operating expenses. This includes preventative maintenance to extend equipment lifespan and reduce downtime.
- Transportation and Logistics Costs: Efficient logistics are critical; transportation costs can range from 3-10% of total operating expenses, impacting the overall supply chain and delivery efficiency.
- Insurance Costs: Protection against potential liabilities and disruptions generally accounts for 2-5% of operational costs, thus safeguarding the business from unforeseen circumstances.
- Waste Management Costs: With sustainability in mind, companies must account for waste disposal which typically represents 2-4% of operating expenses, especially in the context of eco-friendly production.
- Regulatory Compliance Costs: Adhering to industry regulations often incurs costs equating to 1-3% of total expenses, ensuring compliance with local and environmental laws.
- Research and Development Costs: As companies innovate sustainable materials, R&D costs can represent 1-5% of total expenses, crucial for long-term competitive advantage.
Tips for Managing Operating Expenses
- Regularly assess raw material suppliers for cost-effective and sustainable options.
- Implement energy efficiency programs to reduce utilities and energy costs .
- Consider bulk transportation deals to lower logistics costs .
Understanding the cost analysis of building material production can help companies like EcoBuild Innovations strategically manage their operating costs while prioritizing sustainability and efficiency. For further details, consider referencing resources like this article on building material production costs .
Operating Expenses
Operating costs play a crucial role in the financial health of a building material production business. These costs encompass a wide range of expenses that can significantly impact profitability. Understanding and managing these overheads is essential for maintaining a competitive edge in the industry.
Raw Material Costs
In the building material production industry, raw material costs stand out as one of the most significant operating expenses. These costs typically account for up to 50-70% of the total production expenses . For a company like EcoBuild Innovations , which focuses on sustainable alternatives, understanding and managing these costs is crucial for maintaining profitability and competitiveness.
Raw materials required for production can vary widely, depending on the specific type of building materials being manufactured. Common materials include:
- Aggregates (sand, gravel)
- Reinforcing steel
- Wood and timber products
- Sustainable composites and eco-friendly materials
The cost of raw materials can fluctuate based on numerous factors, including:
- Market demand and supply
- Geopolitical events affecting sourcing
- Transportation and logistics costs
- Seasonal variations
Tips for Managing Raw Material Costs
- Establish relationships with multiple suppliers to ensure competitive pricing.
- Invest in sustainable sourcing methods to enhance cost efficiency and reduce waste.
- Utilize technology for better inventory management and to predict raw material needs accurately.
For EcoBuild Innovations , the implementation of sustainable practices not only reduces the environmental impact but can also optimize raw material costs. For instance, utilizing recycled materials can significantly lower expenses while promoting eco-friendly practices. According to a recent study, companies that implemented sustainability measures in their production saw a cost reduction of 15-25% in raw material expenses.
Effective cost analysis of building material production requires thorough tracking of raw material expenses. Leveraging software solutions can help in monitoring price changes and optimizing purchasing decisions. Furthermore, a financial analysis can provide insights into the most cost-effective materials, enabling businesses to make informed choices that align with both budgetary constraints and sustainability goals.
In summary, raw material costs are a major component of the operating costs of a building materials business. By focusing on sustainable sourcing practices, managing supply chains effectively, and utilizing technology, companies like EcoBuild Innovations can significantly influence their overall production costs, thereby enhancing their market position in a competitive landscape.
Labor Costs
In the realm of building material production , labor costs are often one of the most significant components of the overall operational expenditures. Understanding these costs is crucial for effective cost analysis of building material production . Labor is not just about wages; it encompasses a variety of expenses that contribute to the operational efficiency and productivity of the business.
Typically, labor costs in a building material production company can account for approximately 20% to 35% of total production costs. This percentage can vary based on the scale of operations, the degree of automation, and the specific skills required for production processes. Here are the primary elements of labor costs:
- Wages and Salaries: This includes hourly wages for factory workers, technicians, and managerial staff.
- Benefits: Mandatory contributions such as health insurance, retirement plans, and paid leave.
- Training and Development: Ongoing education and skills training for employees to keep up with industry standards.
- Overtime Costs: Additional pay for hours worked beyond the standard schedule, which can significantly impact the bottom line.
Moreover, the skill level of employees greatly influences labor costs. For instance, skilled laborers who specialize in sustainable building materials might command higher wages due to their expertise, which is vital for a company like EcoBuild Innovations aiming to provide innovative and eco-friendly solutions.
Tips for Managing Labor Costs
- Implement automation technologies to reduce reliance on manual labor and lower long-term costs.
- Regularly review staffing needs to align with production demands, avoiding overstaffing during slow periods.
- Invest in employee training to enhance productivity and efficiency, potentially reducing errors and overtime expenses.
It is also important to note the impact of regulatory compliance on labor costs. States may require certain safety standards and training, which can incur additional expenses. This aspect should be carefully factored into the operating costs of a building materials business .
As EcoBuild Innovations strives to create sustainable and eco-friendly building materials, managing labor costs effectively will play a crucial role in ensuring competitiveness while delivering high-quality products. Investing in skilled labor will help achieve a balance between cost efficiency and product innovation, particularly in the evolving landscape of construction material production.
Utilities and Energy Costs
In the building material production industry, utilities and energy costs represent a significant portion of the operating costs of a building materials business . These expenses include electricity, water, heating, and cooling required for various manufacturing processes. For companies like EcoBuild Innovations, focusing on sustainable solutions means that these costs can be both a challenge and an area for potential savings.
According to industry benchmarks, energy consumption costs can account for approximately 20% to 30% of a production facility's total operational budget. The specific percentages can vary based on the type of materials being produced, production scale, and the efficiency of the manufacturing equipment deployed.
To effectively manage these operational costs, building material companies should consider:
Strategies for Reducing Utilities and Energy Costs
- Investing in energy-efficient machinery that consumes less power during production.
- Implementing automated monitoring systems to track energy usage and identify waste.
- Exploring renewable energy sources, such as solar or wind, to offset utility expenses.
- Conducting regular maintenance on heating and cooling systems to ensure optimal performance.
Moreover, understanding operating costs in manufacturing allows for better cost management in construction . For instance, integrating energy-efficient processes not only lowers utilities and energy costs but can also enhance the overall sustainability profile of EcoBuild Innovations.
While fixed costs like building leases remain constant, utilities and energy expenses can fluctuate based on production schedules and seasonal demand. Therefore, a thorough cost analysis of building material production is essential for maintaining profitability.
In terms of regulatory compliance, companies are often required to adhere to specific environmental standards, which can incur additional costs. Understanding the interplay between these compliance costs and utilities can be crucial for building material production businesses in strategizing their operational frameworks.
Maintenance and Equipment Costs
The maintenance and equipment costs represent a significant portion of the operating costs of a building materials business. For a company like EcoBuild Innovations , which aims to provide sustainable alternatives in the building material industry, these costs not only encompass regular upkeep of machinery but also the acquisition and depreciation of advanced equipment designed for eco-friendly production.
In the context of building material production, these costs can broadly be categorized into the following:
- Equipment Purchase Costs: The initial investment in machinery necessary for production can be substantial. Costs often range from $100,000 to $1 million depending on the scale and technology.
- Maintenance and Repair Costs: Regular maintenance is crucial to ensure operational efficiency. The average annual maintenance cost can constitute 3% to 5% of the equipment's value.
- Depreciation: Over time, equipment loses value. Understanding the depreciation schedule can help in cost analysis of building material production.
- Upgrades and Modifications: As technology advances, updating equipment may be necessary to maintain competitive advantage. This could mean additional capital expenditures, which can be 10% to 20% of the initial cost.
- Energy Consumption Costs: Efficient machinery can significantly lower energy costs, often identified as a major portion of production expenses.
Managing these maintenance and equipment costs efficiently is vital for a sustainable business model in the construction material sector. Companies often find that preventive maintenance can lead to long-term savings, reducing unexpected repair costs and maximizing equipment lifespan. The integration of smart technology in machinery may also be seen as a strategy to enhance efficiency and reduce operational costs.
Tips for Reducing Maintenance and Equipment Costs
- Implement a preventive maintenance schedule to avoid costly repairs.
- Invest in energy-efficient equipment to lower energy consumption costs.
- Regularly train staff on proper equipment usage to prevent damage and extend longevity.
To further exemplify the impact of these costs, consider the following breakdown of typical equipment and maintenance costs for a medium-sized building material production company:
As illustrated, the combined maintenance and equipment costs can add significant financial weight to the overall cost structure of a building materials business. Therefore, understanding and strategically managing these operating expenses is crucial for enhancing profitability and ensuring sustainability in the competitive landscape of the construction industry.
For more insights into building a comprehensive financial plan for a building material production business, explore the resources available at Business Plan Templates .
Transportation and Logistics Costs
In the world of building material production , transportation and logistics costs play a critical role in determining the overall operational efficiency and profitability of the business. These costs can significantly impact the cost analysis of building material production as they encompass several key elements related to the movement of products from suppliers to the production facility and from the facility to the end customer.
For a company like EcoBuild Innovations , which focuses on sustainable alternatives, managing these expenses effectively is essential. The transportation and logistics costs typically consist of:
- Freight charges for shipping raw materials.
- Distribution costs for delivering finished products to construction sites.
- Fuel expenses associated with transportation vehicles.
- Maintenance of the transportation fleet.
- Warehousing costs for storage of materials and products.
According to industry benchmarks, transportation and logistics can account for as much as 30% of the total operational costs in the building materials sector. This is why understanding operating costs of a building materials business is crucial in making informed financial decisions.
To successfully reduce these expenses and enhance profitability, businesses in the construction material production arena can implement various strategies:
Tips for Reducing Transportation Costs
- Utilize technology for route optimization to minimize travel time and fuel consumption.
- Consolidate shipments to maximize the load capacity of transport vehicles.
- Build strong relationships with logistics providers for better rates and reliability.
With an increasing focus on sustainability, companies like EcoBuild Innovations must also factor in the environmental impact of their logistics operations. This includes using eco-friendly transport methods and considering local sourcing of materials to minimize transportation distances, thereby reducing both costs and carbon footprint.
In conclusion, understanding and managing the intricacies of transportation and logistics costs is vital for any building material production company striving to remain competitive while maintaining sustainability. By actively engaging in cost management in construction and leveraging technology, businesses can optimize their operations and reduce their overall expenses.
Insurance Costs
In the realm of building material production , insurance costs represent a significant component of the overall operating costs . These expenses are crucial for safeguarding the business against various risks, including property damage, liability claims, and worker-related incidents. For EcoBuild Innovations, a company focused on sustainable building materials, understanding the intricacies of insurance can significantly impact the cost analysis of building material production .
Insurance costs can vary widely based on several factors, including the scale of operations, the types of materials produced, and the company's overall risk profile. On average, construction material production expenses related to insurance can account for approximately 1-5% of total operating costs . This percentage can fluctuate based on the following:
- Type of policies purchased (general liability, property, worker's compensation)
- Geographical location and its associated risks (natural disasters, theft)
- Compliance with industry regulations and standards
For EcoBuild Innovations, investing in comprehensive insurance coverage not only aids in mitigating risks but also enhances credibility with clients and stakeholders. Properly managed insurance can lead to lower operational costs in production through reduced liability exposure and potential claims payouts.
To further manage insurance costs, EcoBuild Innovations can adopt the following strategies:
Tips to Reduce Insurance Costs
- Bundle multiple insurance policies for potential discounts
- Implement safety training programs to reduce workplace accidents
- Regularly review and adjust coverage based on operational changes
Moreover, building materials companies should remain vigilant with risk management practices to keep insurance costs manageable. This can involve conducting routine safety audits and investing in safety equipment, which may ultimately lower premiums over time.
By understanding the implications of insurance costs and implementing smart management strategies, EcoBuild Innovations can achieve a more favorable production cost structure while prioritizing safety and sustainability. This approach not only prepares the business for unforeseen circumstances but also contributes to a robust operational framework that sets the stage for growth in the environmentally conscious construction industry.
Waste Management Costs
In the building material production sector, managing waste management costs is critical for both environmental sustainability and the bottom line. Waste management encompasses the collection, transportation, processing, recycling, and disposal of waste generated during the production process. These costs can significantly impact the overall operating costs of a building materials business , making it essential for companies like EcoBuild Innovations to adopt efficient waste management strategies.
On average, waste management expenses can account for approximately 5% to 10% of the total production costs in the building materials industry. This percentage can vary based on the type of materials produced and the operational practices of the company. Efficient waste management practices not only reduce costs but also enhance the company’s reputation by demonstrating a commitment to sustainability.
Here are some of the key components associated with waste management costs in the industry:
- Collection and Transportation: This includes costs related to the labor and equipment necessary to collect and transport waste materials to disposal sites or recycling facilities.
- Tipping Fees: Facilities charge fees for the disposal of waste, which can vary based on location and type of waste.
- Processing Costs: These are costs associated with sorting and processing recyclable materials, which often require specialized equipment and labor.
- Regulatory Compliance: Adhering to local and national regulations regarding waste management can incur significant costs, including fines for non-compliance.
- Recycling and Recovery: Investing in technologies that allow for the recovery of raw materials from waste can mitigate costs in the long run.
To effectively manage these costs, it is essential for companies to implement waste reduction strategies. These strategies not only contribute to lowering business costs for building material companies but also help in promoting a sustainable production cycle.
Tips for Reducing Waste Management Costs
- Conduct a comprehensive waste audit to identify the types and volumes of waste generated, which can inform targeted reduction strategies.
- Invest in training programs for employees to promote awareness of waste reduction practices and recycling initiatives.
- Collaborate with local recycling facilities to establish efficient processes for waste recovery and disposal.
A cost analysis of building material production should also incorporate the potential savings gained from effective waste management. For instance, companies that successfully reduce waste by just 20% can save thousands of dollars annually, depending on their production scale. Benchmarking these costs against industry standards can provide valuable insights into where improvements can be made.
By strategically managing waste, EcoBuild Innovations can not only reduce operational costs but also enhance its brand image as a leader in sustainable building material production. Understanding the nuances of construction material production expenses related to waste management is essential for financial analysis and operational efficiency.
Regulatory Compliance Costs
Operating a building material production company like EcoBuild Innovations involves significant regulatory compliance costs. These costs are necessary to ensure that the business adheres to local, national, and international laws that govern manufacturing, safety, and environmental impact.
Regulatory compliance costs can include:
- Licensing and Permits: Obtaining the necessary licenses and permits can cost anywhere from $1,000 to $10,000 , depending on the region and the specific materials being produced.
- Environmental Impact Assessments: Conducting assessments to evaluate the environmental effects of production can range from $5,000 to $50,000 , depending on the complexity of the assessment.
- Compliance Audits: Regular audits to ensure adherence to regulations can incur costs between $2,000 and $20,000 annually.
- Training and Certifications: Staff training to comply with safety and environmental regulations may total $3,000 to $15,000 annually.
- Legal Fees: Engaging legal experts for guidance on compliance can result in fees of $200 to $500 per hour, impacting overall operational costs significantly.
In the context of the building materials industry, non-compliance can lead to substantial fines, which can be as high as $100,000 or more, depending on the severity of the violation. Therefore, investing in compliance is not just a legal requirement but a financial safeguard.
Tips for Managing Regulatory Compliance Costs
- Regularly review and update compliance policies and practices to minimize potential fines and penalties.
- Invest in compliance training for employees to reduce the likelihood of violations and associated costs.
- Stay informed about changes in regulations to avoid costly last-minute adjustments.
The regulatory landscape for building material production is complex and continuously evolving. Companies must allocate a substantial portion of their budget to ensure compliance with laws pertaining to health, safety, and environmental protection. According to industry reports, regulatory compliance costs can account for as much as 8-10% of total operating costs in manufacturing, which translates to substantial sums in the context of construction material production expenses.
Furthermore, companies must keep in mind that the cost analysis of building material production should include not just the current regulatory costs but also potential costs related to future regulatory changes. By proactively managing these costs, businesses can maintain a healthy profit margin and ensure sustainable operations that align with EcoBuild Innovations’ commitment to environmental responsibility.
Understanding operating costs in manufacturing, such as regulatory compliance costs, is essential for effective financial planning and resource allocation in building material production. This careful management can lead to significant savings, reinforcing the importance of a robust regulatory strategy.
Research and Development Costs
In the ever-evolving world of building material production , the significance of research and development (R&D) cannot be overstated. For a company like EcoBuild Innovations, which is dedicated to providing sustainable alternatives in the construction sector, R&D costs represent a critical segment of the overall operating costs . These expenses are essential for driving innovation and ensuring that products remain competitive in a market increasingly driven by environmental considerations.
R&D costs in the building material production landscape can typically account for approximately 5% to 15% of total production expenses, depending on the company's focus on innovation and the complexity of materials being developed. For instance, using advanced technologies to create eco-friendly concrete or insulation materials entails significant investment in research, testing, and development.
Managing these R&D costs effectively is crucial for maintaining profitability while driving innovation. Companies should always focus on the cost-benefit analysis of their research projects to ensure they are investing wisely and generating tangible outcomes.
Tips for Managing R&D Expenses
- Prioritize projects with clear market demand and potential returns.
- Utilize partnerships with universities and research institutions to share costs.
- Implement a phased approach to R&D investments to mitigate risks.
In addition to direct costs, companies must also consider indirect costs associated with R&D. This includes overhead costs related to facilities where research is conducted, as well as capital expenditures for maintaining state-of-the-art equipment necessary for testing and development. Understanding the nuances of these expenses is vital for a comprehensive cost analysis of building material production .
Ultimately, the operating costs of a building materials business hinge significantly on effective R&D investment strategies. In the pursuit of creating innovative, eco-friendly solutions, managing these costs while maximizing output can give companies like EcoBuild Innovations a solid competitive edge in the market.
- Choosing a selection results in a full page refresh.
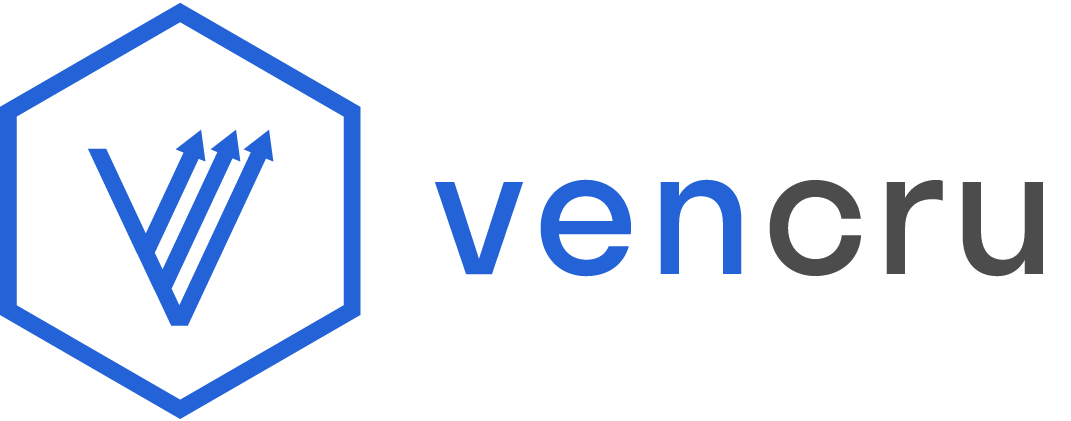
How to Calculate Cost of Materials
- October 4, 2024
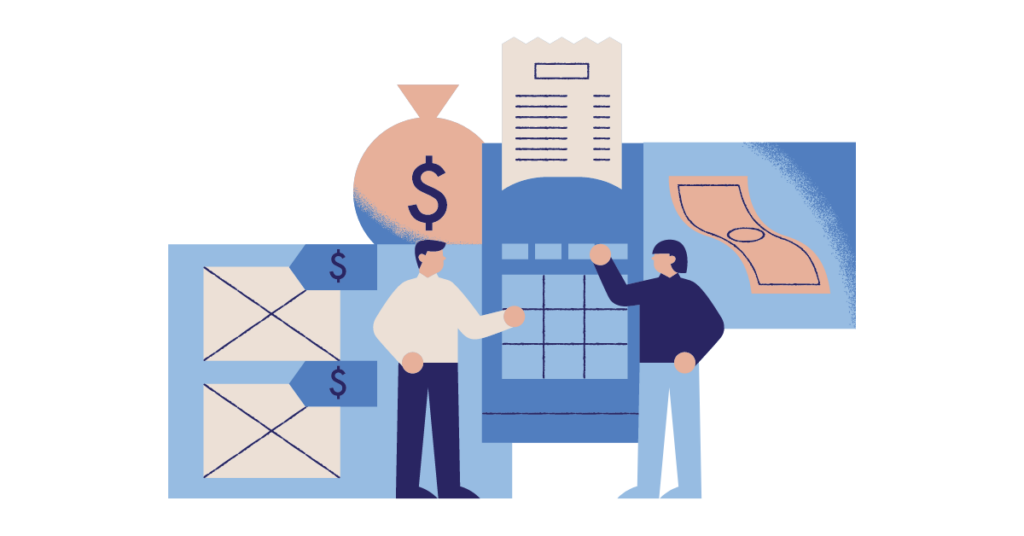
Table of Contents
Manage your inventory and business easier, get started for free.
Accurately calculating the cost of direct materials is essential for businesses that manufacture products or handle inventory. Understanding direct material costs helps in budgeting, pricing, and maintaining profitability. Whether you’re a small business owner or a supply chain manager , knowing how to calculate direct materials used effectively can drive better financial decisions and operational efficiency. In this blog, we’ll explore the methods for calculating direct material costs, the factors to consider, and how to apply these calculations in real-world scenarios to enhance your financial management. We’ll be discussing:
- What is the Cost of Materials?
- Why Calculate the Cost of Materials
- Factors to Consider in Material Cost Calculation
Example of Cost of Materials Calculation
What is the Cost of Direct Materials?
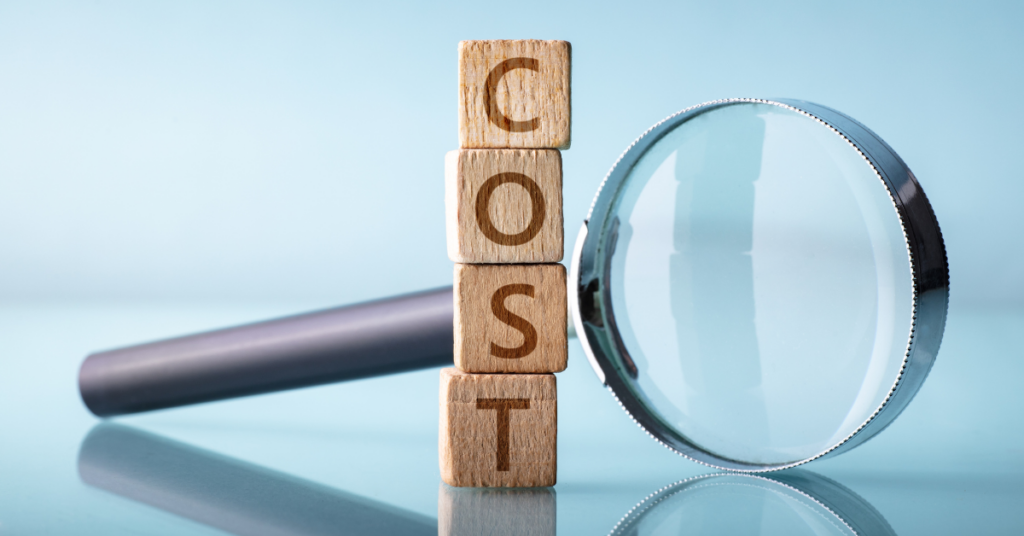
The cost of direct materials refers to the total expense incurred to acquire raw materials or components used directly in the production of goods. It includes not just the purchase price of the materials but also any additional costs associated with acquiring and handling them. Accurate direct material cost calculation ensures that you price your products correctly and manage your inventory efficiently, which is crucial for maintaining a healthy bottom line.
Why Calculate the Cost of Direct Materials?
Understanding direct material costs is crucial for several reasons:
- Accurate Pricing: Knowing the precise cost of direct materials helps in setting accurate prices for your products. It ensures that you cover costs and achieve desired profit margins. Furthermore, it avoids the pitfalls of underpricing and helps maintain a competitive edge in the market.
- Budgeting and Forecasting: Calculating direct material costs not only aids in creating realistic budgets and forecasts, but also is essential for financial planning and resource allocation. Moreover, accurate cost estimates help prevent budget overruns, thereby supporting strategic decision-making.
- Cost Control: By tracking direct material costs, businesses can identify areas where they can reduce expenses, negotiate better prices with suppliers, or find more cost-effective materials. Effective cost control measures improve overall profitability and operational efficiency.
- Inventory Management: Accurate direct material cost calculations assist in managing inventory levels, reducing waste, and optimizing stock levels. Proper inventory management ensures that resources are used efficiently and that production runs smoothly.
Factors to Consider in Direct Material Cost Calculation
When calculating the cost of direct materials, several factors should be taken into account:
- Purchase Price: The base cost of acquiring the raw materials or components from suppliers. This is typically the amount listed on purchase invoices and forms the foundation of direct material cost calculation.
- Shipping and Handling: Costs associated with transporting and handling materials, including freight charges, packaging, and delivery fees. These costs can add significantly to the total direct material cost and should be carefully considered.
- Taxes and Duties: Any applicable taxes or import duties that are added to the cost of materials, especially for international purchases. These charges can vary based on the product’s value, weight, or classification and can impact overall costs.
- Insurance: Costs associated with insuring materials during transit. Insurance protects against potential loss or damage and is an important factor in calculating the total cost of direct materials.
- Storage Costs: Expenses related to storing materials, such as warehousing fees or costs of maintaining inventory. Effective management of storage costs helps in optimizing inventory and reducing overheads.
- Labor Costs: If applicable, include the cost of labor for handling, processing, or preparing materials. Labor costs can affect the overall direct material cost and should be factored into the calculation.
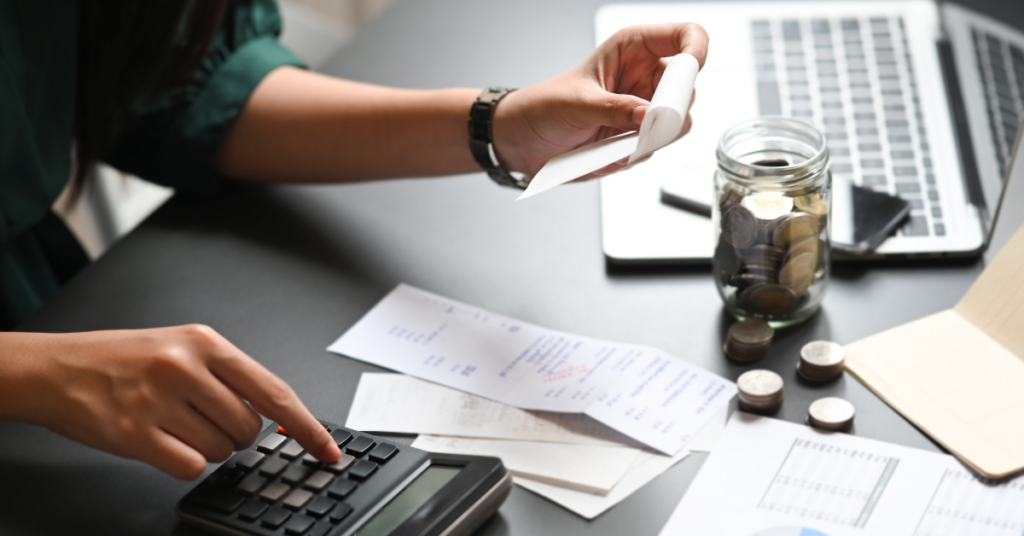
How to Calculate Direct Materials Used
Here’s a step-by-step guide on how to calculate direct materials used:
Example Calculation: Total Cost of Direct Materials Used=Total Purchase Price+Total Shipping and Handling Costs+Taxes and Duties+Storage Costs+Labor Costs Total Cost of Direct Materials Used=$500+$70+$30+$40+$60=$700
Determine the Purchase Price:
Start with the base purchase price of the materials. This is the amount you pay the supplier for the materials and represents the initial cost of acquisition.
Example: If you buy 100 units of material at $5 per unit, the total purchase price is: Total Purchase Price=100 units×$5/unit=$500
Add Shipping and Handling Costs:
Include all costs associated with transporting and handling the materials. This could involve freight charges, packaging, and delivery fees, which contribute to the total cost of direct materials.
Example: If shipping costs are $50 and handling fees are $20, the total shipping and handling cost is: Total Shipping and Handling Costs=$50+$20=$70
Include Taxes and Duties:
Add any taxes or import duties that apply to the materials. These charges can impact the overall cost and should be included in the total direct material cost calculation.
Example: If the tax and import duty amount to $30, add this to the total.
Account for Storage Costs:
Include costs related to storing the materials in your warehouse. Properly accounting for storage costs helps in managing inventory efficiently.
Example: If monthly storage fees are $40, include this cost.
Add Labor Costs (if applicable):
Include any labor costs associated with handling or processing the materials. Labor costs can influence the overall direct material cost and should be factored into the calculation.
Example: If labor costs for handling the materials are $60, add this to the total.
Calculate the Total Cost of Direct Materials Used:
Sum up all the costs to arrive at the total cost of direct materials. This comprehensive total reflects the complete expense incurred to acquire and manage the materials.
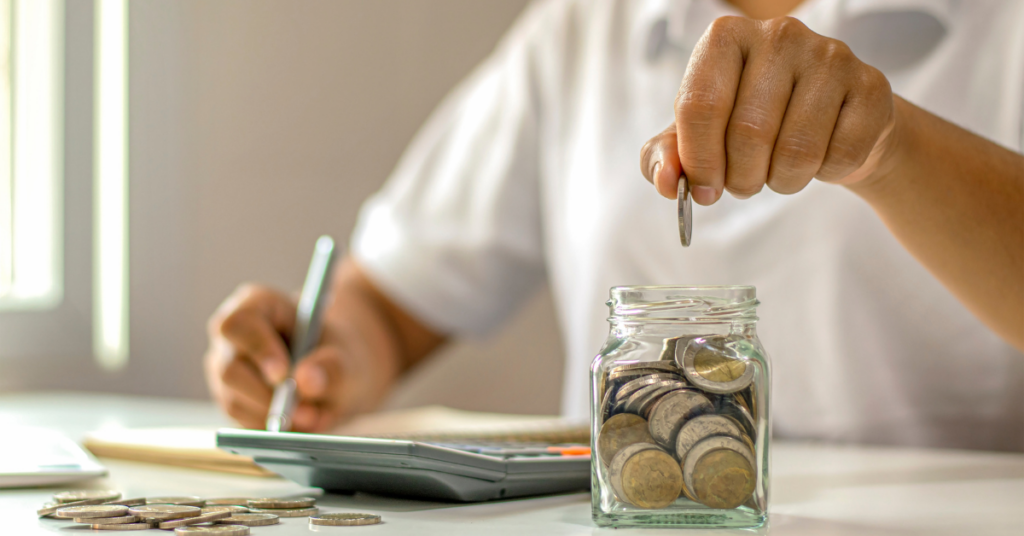
Let’s say you’re calculating the cost of materials for a batch of products:
- Purchase Price: $500
- Shipping and Handling: $70
- Taxes and Duties: $30
- Storage Costs: $40
- Labor Costs: $60
The total cost of materials would be: $500+$70+$30+$40+$60=$700
Thus, the cost of materials for this batch is $700.
Calculating the cost of materials is a critical aspect of managing production costs and pricing products effectively. By considering all relevant factors—such as purchase price, shipping costs, taxes, storage costs, and labor—you can arrive at an accurate material cost. Consequently, this knowledge enables better budgeting, pricing, and cost control, which ultimately contributes to improved profitability and operational efficiency.
Furthermore, mastering material cost calculations is essential for making informed financial decisions and maintaining a competitive edge in the market. By following these steps, you can ensure that your material costs are accurately accounted for, which leads to better financial management and success in your business endeavors.
Related Content
- What is Minimum Order Quantity (MOQ)?
- What is a Distributor?
- What Is Deadstock?
- What Is Freight? Definition and Meaning
- Inventory Valuation Methods: Which One Should You Choose?
Latest blog posts
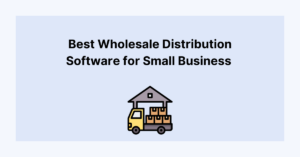
Best Wholesale Distribution Software for Small Businesses
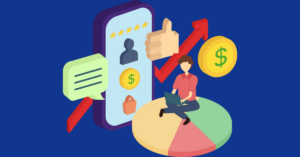
5 ways Businesses Can Generate Sales Using Social Media
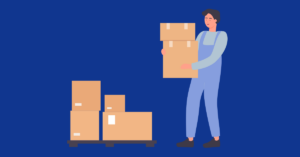
Roles and Skills Required in Warehouse Management
Subscribe to our newsletter, get updates and learn from the best, manage your inventory and bookkeeping easier.
Track sales, inventory, and expenses easier with Vencru. Get real-time accurate reports and insights from anywhere.
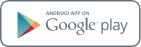
Simple inventory and accounting software for your small, medium, or large business
Free resources
Get the app.
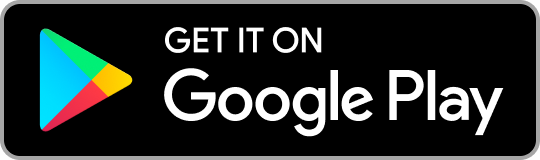
© 2024 Vencru Inc. All rights reserved.
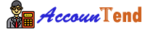
Understanding Materials Cost: Definition, Importance, and Examples
Introduction to Materials Cost
Materials cost is a crucial concept in business and finance. It refers to the expenses a company incurs in acquiring the raw materials needed for production. These costs play a significant role in determining a company’s profitability and competitiveness in the market.
Definition of Materials Cost
Materials cost encompasses the expenditure associated with purchasing raw materials, components, and supplies necessary for manufacturing goods or providing services. It includes the cost of procuring materials from suppliers, transportation expenses, import duties, and any other expenses directly related to obtaining the required materials.
Importance of Materials Cost
Understanding materials cost is essential for businesses for several reasons:
- Cost Control: Materials cost represents a significant portion of a company’s expenses. By effectively managing these costs, businesses can improve their profit margins and overall financial performance.
- Product Pricing: The cost of materials directly impacts the pricing strategy of a product or service. A thorough understanding of materials cost enables businesses to set competitive prices while ensuring profitability.
- Inventory Management: Efficient materials cost management helps in optimizing inventory levels. By maintaining an appropriate balance between supply and demand, businesses can reduce storage costs and avoid stockouts or overstock situations.
- Quality Control: The quality of raw materials directly affects the quality of the final product. Investing in high-quality materials, while controlling costs, is essential for delivering products that meet customer expectations and satisfaction.
Calculating Materials Cost
To calculate materials cost, businesses typically consider the following factors:
- Direct Material Costs: This includes the actual cost of raw materials required for production. It involves identifying the quantity of materials needed for each unit of production and multiplying it by the unit cost.
- Indirect Material Costs: Indirect material costs refer to expenses associated with materials indirectly used in production, such as lubricants, cleaning supplies, and small tools. These costs are usually allocated based on usage or production volume.
- Transportation and Handling Costs: Businesses need to account for transportation and handling expenses incurred in procuring materials from suppliers and delivering them to the production facility. These costs may include shipping fees, customs duties, and storage charges.
- Waste and Spoilage: Businesses must also consider the potential waste or spoilage of materials during the production process. Factoring in the expected loss allows companies to adjust their materials cost estimates accordingly.
Example of Materials Cost
Let’s consider an example to illustrate how materials cost is calculated:
Suppose a furniture manufacturing company produces wooden chairs. To manufacture one chair, it requires:
- 5 feet of wood costing $10 per foot
- $2 worth of screws and bolts
- $3 for transportation and handling
Therefore, the direct material cost per chair would be: 5 feet \times $10/foot + $2 + $3 = $55
In this example, the materials cost per chair is $55.
Materials cost is a fundamental aspect of business operations, particularly in manufacturing and production industries. By understanding and effectively managing materials cost, businesses can improve their competitiveness, profitability, and overall financial performance. It is essential for companies to accurately calculate and monitor materials cost to make informed decisions and optimize their resource utilization.
Related Posts
Written-down value (wdv) explained for beginners.
If you’re new to finance and accounting, terms like “Written-Down Value” or WDV might sound…
Activity Sampling (Work Sampling): Unveiling Insights into Work Efficiency
Activity Sampling, also known as Work Sampling, is a method used in various industries to…

COMMENTS
Material Cost: Definition. Material is the most important element of cost. In most manufacturing organizations, 50% to 70% of the total cost of a product is represented by the cost of the material. Material cost was defined by the Institute of Cost and Management Accountants as follows: "the cost of commodities supplied to an undertaking."
Depending on the objective of the business plan, these costs may include the cost of purchasing the raw material, the cost of marketing, or even the cost of packaging the finished products. Note that starting or running a business will involve some kind of cost, and this is what is noted in the cost structure of the business plan.
Raw materials are often referred to as commodities, which are bought and sold on commodities exchanges worldwide. Raw materials are bought and sold in what is called the factor market because raw materials are factors of production along with labor and capital. Table 6 Raw Materials. Particulars Qty. Unit of. Measurement. Unit Cost Total Cost
The three basic categories of product costs are detailed below: 1. Direct material. Direct material costs are the costs of raw materials or parts that go directly into producing products. For example, if Company A is a toy manufacturer, an example of a direct material cost would be the plastic used to make the toys. 2. Direct labor
Material cost is calculated by summing up the costs of raw materials used in production, taking into account inventory levels and accounting for these expenses in the overall business costs. This calculation process involves tracking the purchase price of raw materials, transportation costs, storage expenses, and any additional costs incurred ...
Material Costs: The raw materials required for production vary with the quantity of items being machined. For example, if a company produces 1,000 components, the material cost might be around $10,000, while a production run of 5,000 components can escalate this cost to approximately $50,000.
This is part 11 / 12 of Write Your Business Plan: Section 5: Organizing Operations and Finances series. Manufacturers combine labor and materials to produce products.
Operating Costs Examples For A Building Material Production Company. When launching a business in building material production, understanding the operating costs is crucial for profitability and sustainability. The costs associated with running a business like EcoBuild Innovations include a variety of fixed and variable expenses that can greatly influence the cost analysis of building material ...
Include any labor costs associated with handling or processing the materials. Labor costs can influence the overall direct material cost and should be factored into the calculation. Example: If labor costs for handling the materials are $60, add this to the total. Calculate the Total Cost of Direct Materials Used:
Introduction to Materials Cost Materials cost is a crucial concept in business and finance. It refers to the expenses a company incurs in acquiring the raw materials needed for production. These costs play a significant role in determining a company's profitability and competitiveness in the market. Definition of Materials Cost Materials cost encompasses the expenditure […]